Content
The goal of a functional prototype is to fail fast by testing early and often through iterative design. Potential applications include testing aerodynamics, mechanical performance, mechanical properties, and thermal performance. For this phase of prototyping, investments are better applied at the beginning, rather than towards the end of the process – when mistakes can cost more to correct. Fortunately, there are a variety of rapid prototyping processes today that are capable of building functional prototypes quickly, cost-effectively and with high precision. Prototyping is the process by which design teams convert ideas from paper to digital. To capture design concepts and test them on users, teams create prototypes of varying fidelity.
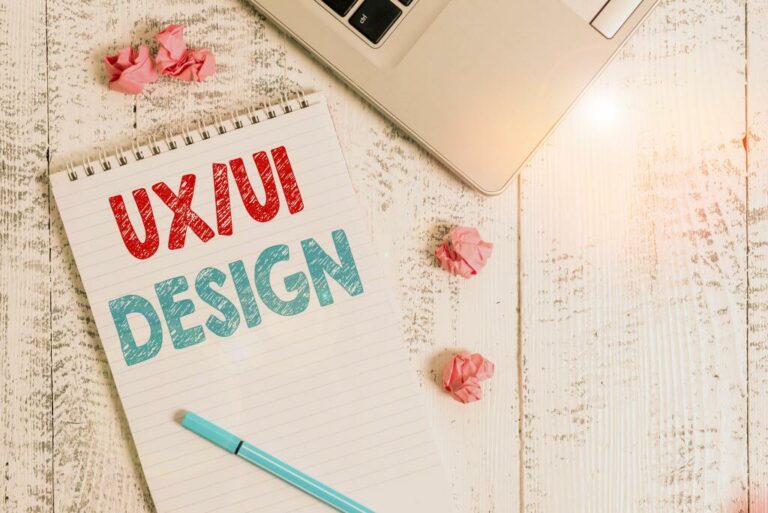
It outlines the basic layout of your app without written content or visual elements. You can think of your wireframe as a rough roadmap for where you’d like to go with your project. Your wireframe will function as the blueprint for your low or high-fidelity prototypes. It’s typical to employ the concepts of design thinking at this early design stage, going through many iterations before choosing one to move forward to the next stage. The functional prototype is where the proof of concept meets the industrial design. This is a product that could be shared directly with a stakeholder to use and provide feedback against.
If manufacturing cannot be scaled, manufacturers may use pilot prototypes in soft launches. It is quickly developed to show how the need https://globalcloudteam.com/ will appear visually. Customer feedback aids in the movement of demand change, and the prototype is re-created until the need is basic.
Design Iteratively and Instantly Incorporate Changes
Laser cutters use a laser to engrave or cut through a wide range of materials with high precision. Water jet cutters use water mixed with abrasive and high pressure to cut through practically any material. CNC milling machines and lathes can have multiple axes, which allows them to manage more complex designs.
Inaccurate feedback from users due to lack of realism in the experience. Users may “fill in the gaps” in ways that are different than what the designer has in mind, therefore impacting results. Paper prototypes are a great team-building exercise, resulting in increased involvement, ownership, and empathy towards the users and product. Prototypes allow designers to engage with stakeholders and end users, which gives them the chance to become involved in the process and feel a sense of ownership. This will potentially aid in their “buy-in” and help push the concept forward faster.
The order process, tax issue and invoicing to end user is conducted by Wondershare Technology Co., Ltd, which is the subsidiary of Wondershare group. Kerning allows designers to control the amount of space between letters in typography. If you’d like to learn how to prototype with Adobe XD, check out this recording of a recent event we held to walk through this process. No matter how thorough your UX research is, many people find it difficult to truly conceptualize a product until they have it in front of them.
Therefore, pinpoint key features you wish to spotlight in this discovery session. When a user thinks you have spent a long time on something, they may “settle” and not speak up as much as they would when interacting with a paper prototype. This enables the designer to test the core usability of the product prior to beautifying the product. Prototyping can range in method and technique, which is often referred to as low, medium, or high fidelity. Fidelity refers to the level of detail and the functionality of your prototype.
Iterative Prototyping
A pilot prototype will traditionally be provided to independent testing labs responsible for issuing product certifications. Once these final certifications have been received, the product can be considered ready for commercial deployment. The appearance prototype is visually representative while lacking actual functionality. It’s a static model without working features, wholly concerned with providing a sense of the look and feel.
- Because the process starts with a solid block of material, the final result is generally much stronger and smoother than what can be achieved with a 3d printer.
- Selective Laser Sintered 3D printed nylon is a valuable tool for building a proof of concept design, fixtures, and other features because of its low cost across various geometries.
- At this point, the prototype still does not have the cost benefit of mass-produced components, meaning the use of the final materials may be prohibitively expensive.
- You can learn more about how to test your prototypes in this guide.
- For example, PolyJet 3D printing can create rubber-like parts, and SLA has several materials that simulate injection molded pieces.
- The goal is to test the functionality of the product before a further investment into higher-grade materials is made.
The first physical model created along the product roadmap is the proof of concept prototype. ”, it is strictly concerned with function over form and will likely bear little if any resemblance to the final product. Answering these questions usually necessitates two separate prototypes, each one specifically created to address basic functionality prototype of a website and user experience respectively. We can refer to these first two as the proof of concept and the appearance prototypes. The presentation stage will differ based on the purpose of the prototype. It may include creating multiple models for testing among consumers, sending the design in for patenting, or showing it to potential investors.
They start with solid blocks, bars, or rods of plastic, metal, or other materials that are shaped by removing material through cutting, boring, drilling, and grinding. FDM has the lowest resolution and accuracy when compared to other plastic 3D printing processes and is not the best option for printing complex designs or parts with intricate features. Higher-quality finishes may be obtained through chemical and mechanical polishing processes.
Rapid Prototyping Tools and Methods
Typically, the higher the fidelity, the more effort and cost it takes to create. Different scenarios call for different levels of fidelity, and there are pros and cons of each. Best practices include knowing what each includes, as well as how and when to use them. Prototypes allow designers to experiment with various ideas and solutions. They give the designer freedom to test multiple potential scenarios, while adjusting along the way to optimize the usability of the end product. Design thinking is both an ideology and a process used to solve complex problems in a user-centric way.
They limit the design to user flows and information architecture while omitting branding elements, photos, and logos. If that sounds vague, it’s because they can take on many different forms. Whether we’re designing services, apps, physical products, or strategy, prototypes continually serve as invaluable tools for testing and improving upon design concepts. Prototyping and testing go hand in hand, so once you’ve created a prototype, you’ll need to put it in front of real users.
It is very common to be working on two different product designs in parallel later in the product development cycle. One version of the product design is used for prototype testing and design validation. This concurrent engineering approach, while resource intensive, yields the lowest risk approach and the fastest time to market. The fourth and final step of both design thinking and design sprints is prototyping. It’s the next step in the UX design process after “ideation,” where you and your team come up with ideas to address user needs.
Get XD Ideas delivered to your inbox. Free.
This phase typically occurs early in the product development lifecycle, and the aim is to build either a one-off piece or several pieces quickly. During the medical device design process, engineers will spend countless hours prototyping by creating specifications, designing CAD drawings, and manufacturing physical products. These prototypes and their iterations are essential to the development of the device. With each prototype, the design of a medical device gets one step closer to the medical tool that eventually ends up in the hands of surgeons, patients, or healthcare providers. When all the tasks related to empathizing and defining in design thinking process are finished there is a time for the next important stage in which all the ideas should find their first visible form.
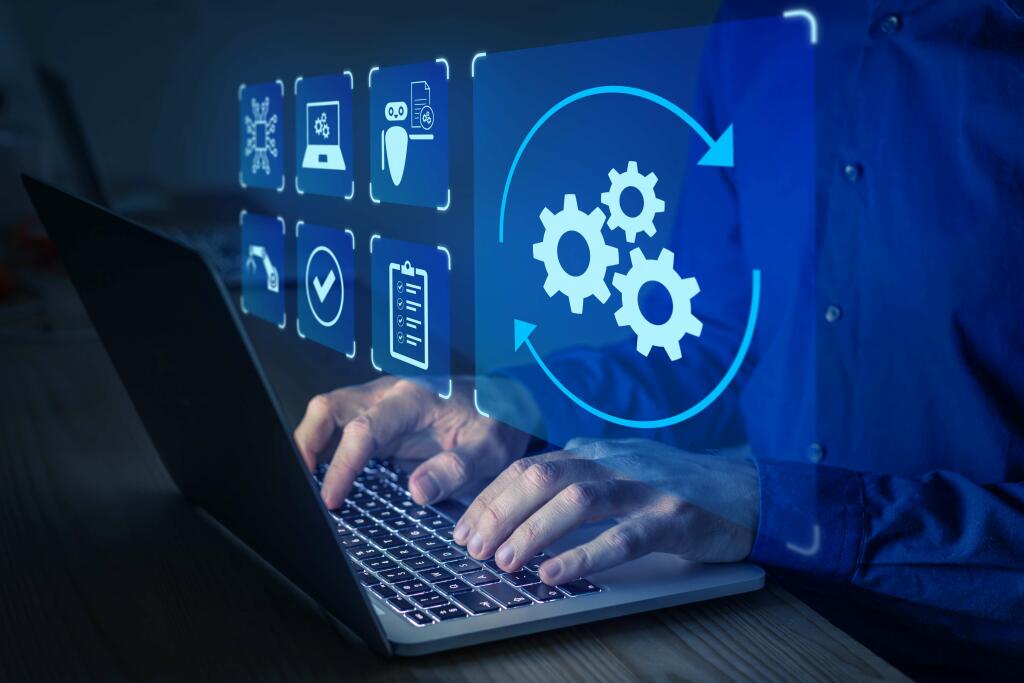
DeviceLab has the resources to guide your product development team through prototype development and finalize your product’s design. Contact DeviceLab today to schedule a consultation and to learn more about our services. Once the device design has gone through a few iterations of beta prototyping, then engineers might begin pilot prototyping. Pilot prototypes are refined beta prototypes that resemble the final, finished medical device. Once the design is finalized, pilot prototypes will be used in verification and validation testing. Verification and validation testing data is part of the evidence that is sent to the FDA as proof of the device’s safety and efficacy.
The 5 Stages of Prototyping
SLA 3D printers use a laser to cure liquid resin into hardened plastic in a process called photopolymerization. SLA is one of the most popular processes among professionals due to its high resolution, precision, and material versatility. Engineers at Wöhler built a looks-like, works-like prototype of a moisture meter from multiple materials with rigid housing and soft-touch buttons. Looks-like, works-like prototype of a moisture meter from multiple materials with rigid housing and soft-touch buttons. Looks-like prototypes of the Form 2 SLA 3D printer with different solutions for cartridge placement.
Useful Tips for Prototype Development
Functional prototypes are typically still made before any major investments in production tooling to mitigate any costly mistakes or revision changes down the line. With 3D printing and online manufacturing services, it has never been easier to produce a prototype quickly and cheaply. Many engineers know that prototyping is not just for earlyrapid prototype development, but can also play a role throughout various phases of validating a new product. From engineering to sales to market research, having an updated prototype in hand can be immensely valuable to achieving the best project results.
Low-fidelity prototype is a simple, interactive version of your product. Your low-fi prototype establishes the placement and size of various elements, and includes navigation and basic clickability. Most content integrated at this stage will function as a placeholder, so don’t be surprised if you see generic content in this stage of app prototyping. If you’re trying to test out a new combat system, you do not need to build the entire exploration system. If you’re making a card game, hand writing on index cards is faster to make than typing everything into Powerpoint, printing on heavy card stock, and cutting it all out manually. There is a time and place for making nice-looking components, and the early stages of game design isnotthat time or that place.
Step 2: Quickly Designing the Prototype
SLS 3D printers use a high-powered laser to fuse small particles of polymer powder. The unfused powder supports the part during printing and eliminates the need for dedicated support structures. This makes SLS ideal for complex geometries, including interior features, undercuts, thin walls, and negative features. Parts produced with SLS printing have excellent mechanical characteristics, with strength resembling that of injection-molded parts. With Draft Resin, SLA 3D printing is also one of the fastest prototyping tools, up to 10X faster than FDM 3D printing.
A prototype can be a limited-functionality software performance model. There are multiple tools, which can be used for prototyping, hence our designing efforts should be saved for future reference. Careful selection of forms best suited for our project seem to be similarly important. Each stage of the prototype creation may be filmed and photographed for the future reference – the values emerging during the prototyping stage may be kept and later presented to the broader audience when needed. Mock up or almost-working model are enough to verify their attractiveness for potential user. This isn’t often talked about in the design forums that I frequent, but it is a vitally important option.